Progressive Die Stamping of Fiber Optic Connectors for the Electrical Industry
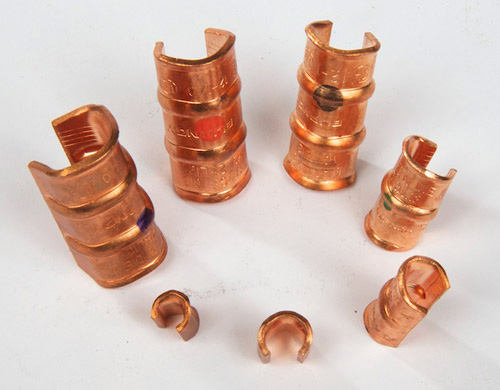
PROJECT DESCRIPTION
The connector shown here was designed for use in a fiber optics application, and required completion of stringent UL testing. Composed of C110 copper alloy, manufacturing required progressive die stamping, which was performed on our 150 Ton Minster straight side press, and included deburring and bright dipping. This precision component required tolerances of ±0.005″, and angular tolerances of ±0.5°, which we meet throughout the 400,000 parts produced annually.
Our reputation as a manufacturer of precision die stamped products, is what brought this customer to us. This project consists of 10 different components, all manufactured to the same tight tolerances, and short lead times. At ART we have the ability to provide our customers with value added services and capabilities that result in quality products, delivered at competitive process. To learn more about this project, see the table below or contact us directly.
Highlights of this Progressive Die Stamped Copper Connector
This connector is used to allow a simple fiber optic connection.
Primary:
Progressive Stamping
Secondary:
Deburring
Bright Dipping
150 Ton Minster Straight Side Press
Length: 0.40″ to 1.75″
± 0.005″
Angular: ± 0.5°
Copper C110
Bright Dip
UL Testing
Electrical Industry
400,000 per year
Initial Project: 22 weeks
After Die Completion: 4 weeks
Customer supplied print, 2D CAD Drawing
Fiber Optic Connector